Our current innovation projects
TRL9 Limited has a risk based, balanced portfolio of research and development projects. Our projects are categorised by Technology Readiness Levels (TRLs) and their proximity to a product market launch and include fully commercialized products, near to market products and future research and development projects.
High Entropy Alloys
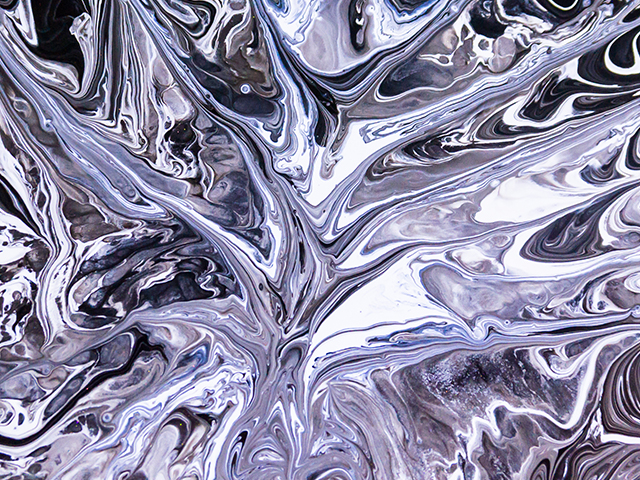
Innovate UK Project Number: 53662
Overview: Design of High Entropy Superalloys using a hybrid experimental-based machine learning approach. Steel Sector Application.
This project utilises a series of innovate algorithms to select the functionality of a High Entropy Alloy. The alloys are formed by mixing equal or relatively large proportions of (usually) five or more elements. Prior to the synthesis of these substances, typical metal alloys are comprised of one or two major components with smaller amounts of other elements which are subsequently pulverised and applied as a powder using high velocity oxy-fuel coating techniques. This provides a protective coating on equipment such as copper moulds in the steel manufacturing industry.
Solid State Heat Engines
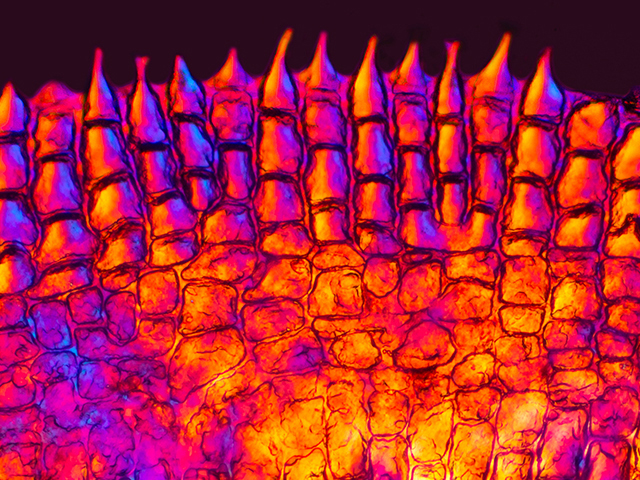
Overview: Feasibility study.
This is a self-funded study into the feasibility of combining several thermo-electric materials with different temperature signatures to form a Solid-State Heat Engine. The Solid-State Heat Engines are used for scavenging waste heat from industrial processes such as steel making, glass making and residual heat from a power station economiser.
Wearable Thermo-electric Devices
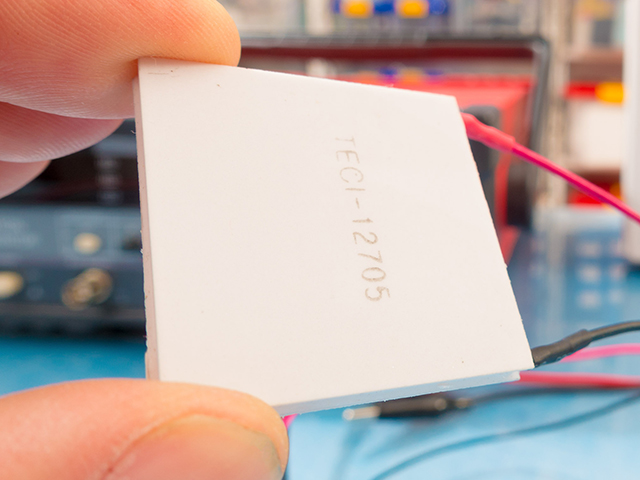
Overview: 3D assembled thermoelectric polymer devices for energy scavenging.
This is a PhD project in collaboration with Durham University. The project explores the use of thermo-electric polymer blends to form a device where the polymers are shaped in 3D in such a way that the thermo-electric junctions required for a Thermo-Electric Generator can be assembled using an interlocking ('Lego' brick) style approach. This approach will lead to a low cost of manufacture. Elastomers such as Polydimethylsiloxane(PDMS) are well suited for such applications and the team at Durham University has long standing expertise in the production of PDMS 3D stamps for applications such as microfluidics, terahertz component production and for nanoimprint lithography.
The aim of this program is to develop a wearable material or device capable of charging a smart watch or smart phone by simply using the heat from your body.
Air Sterilisation and Air Shield
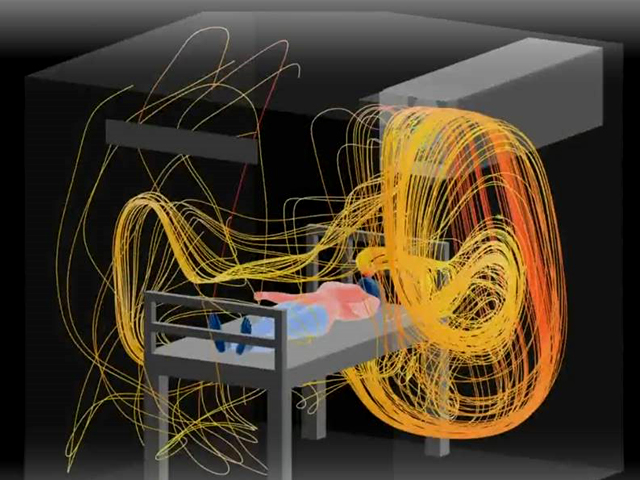
Overview: COVID-19 response project.
In response to the COVID-19 pandemic, TRL9 Limited has developed an air sterilisation system capable of neutralising Corona virus pathogens by fusing protein stems which makes them inactive. The air sterilisation system works by drawing contaminated air through a N97 HEPA filter and then creating a Dean Vortex (a type of motion that is expected to appear as a pair of counter-rotating cells) over a series of ultraviolet, spectrally selective elements. This system targets the virus even if it is attached to a microscopic dust particle. In addition, the system continually processes the air in a space, place, or face device (the air shield) changing the air in each space up to 10 times in an hour. An air space might be inside an aeroplane, a train or a bus, a place might be a room in an office, school, surgery or pub and the face device might be a face covering or mask. This is the first innovation to treat 100% of the air with a highly targeted UV wavelength providing and maintaining a COVID free environment.
Solar Fluidics
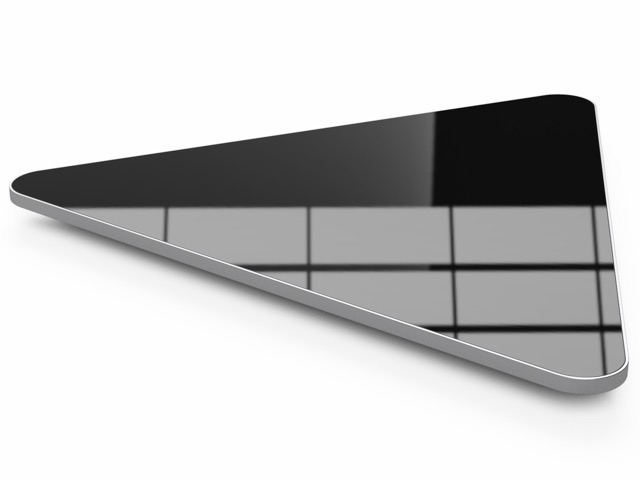
Overview: A revolutionary new solar panel that combines both thermal and photovoltaic power.
A solar cell, or photovoltaic cell, is an electrical device that converts the energy of light directly into electricity by the photovoltaic effect, which is a physical and chemical phenomenon. This is an innovation in portable, combined heat and power generated from the sun. This technology is different to the typical solar panels seen on the roofs of buildings which are permanent fixtures, stationary and expensive to install. Each panel assembly can provide enough hot water and electricity to service a typical 2-bedroom house, replacing the need for natural gas and providing full functionality in remote and off-grid environments. Humanitarian applications in Sub-Saharan Africa and the Middle East already exist and prototype installations are now appearing in remote Northumberland. The panel assembly incorporates the latest cyber-physical connectivity enabling a ‘Plug and Play’ system which is both cost effective and portable.
Further development of the Solar Fluidics system is currently underway and will provide a water purification system and de-salination system for Middle East and Asian applications. For further information visit the Solar Fluidics website for a full description of the product: https://solarfluidics.com/
brOWSER project (Oleophobic Surfaces)
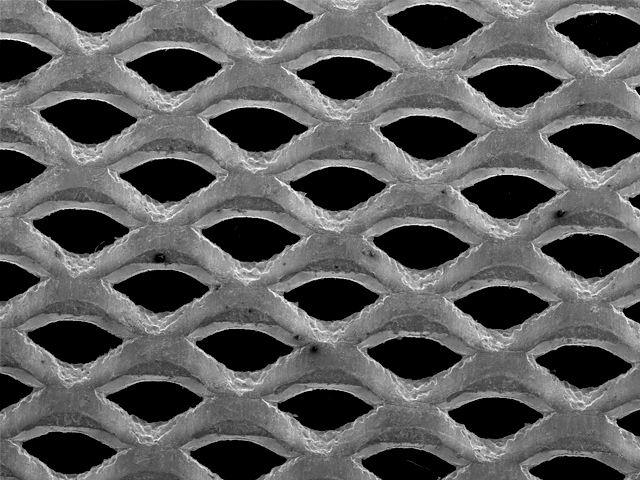
Innovate UK Project Number: 72516
Overview: brOWSER 2D materials for efficient industrial oil and water separation.
This is an Innovate UK funded project to investigate robust oil – water emulsion separation. A metallic mesh is coated with a nano-particulate based on tungsten which allows for the efficient separation of oil and water emulsions. The brOWSER system, currently a working prototype has diverse applications from the food industry to the oil and gas industry. The formidable nature of the brOWSER system lends itself to the clean-up of oil spills and the system can be scaled up to deal with ocean pollution from crude oil.
Down-Hole Oil Industry Wear Coatings
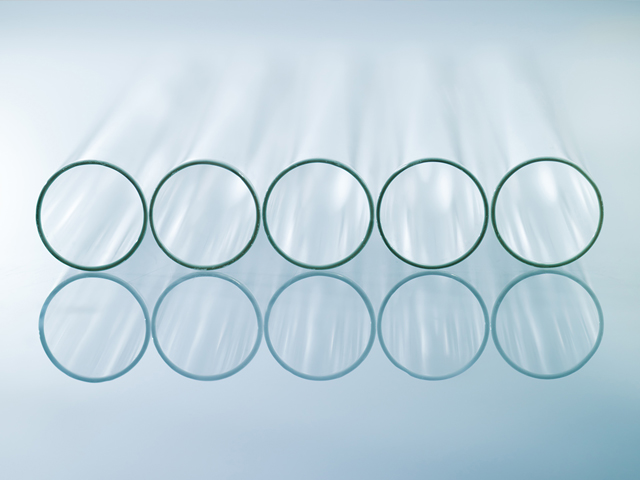
Overview: Third generation cost effective, eco-friendly coatings.
Mud motor rotors and other down-hole tools have seen a transformation from chrome plating to tungsten carbide cermet coatings. This third-generation coating flips the common misconception that hard coatings are better for wear resistance when tested to the ASTM G65-16e1 standard. TRL9 Limited has developed a fluorinated polymer coating which provides better wear and corrosion resistance than the current state-of-the-art carbide-based coatings. Our new coating is highly cost effective and completely recyclable.
Steel Industry Mould Coatings: Remote Digital Manufacturing
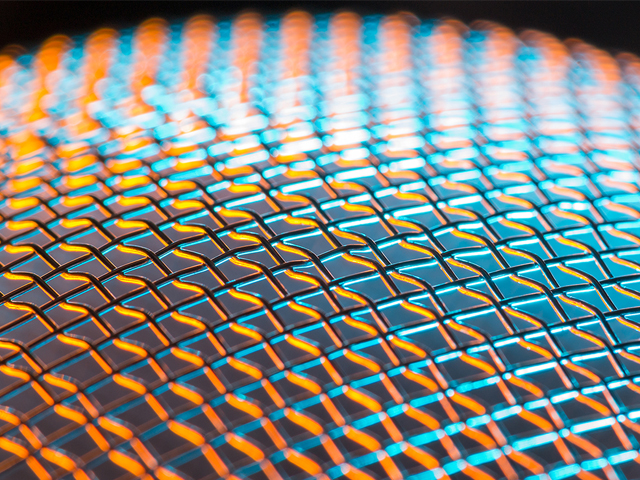
Innovate UK Project Number: 79075
Overview: Remote manufacturing process monitoring, control and troubleshooting through machine learning in an Industrial Internet of Things (IIoT) application.
This is one of the first truly digitally controlled surface engineering applications. A series of algorithms drives machine learning in an Industrial Internet of Things (IIoT) application. TRL9 Limited has co-designed a digital twin of a thermal spray coating system which can be remotely monitored and controlled to apply high wear and chemical resistant coatings on the internal dimensions of billet moulds for the steel industry. Cyber-physical connectivity allows simultaneous control and deployment on opposite sides of the world.
Aircraft Carrier Deck
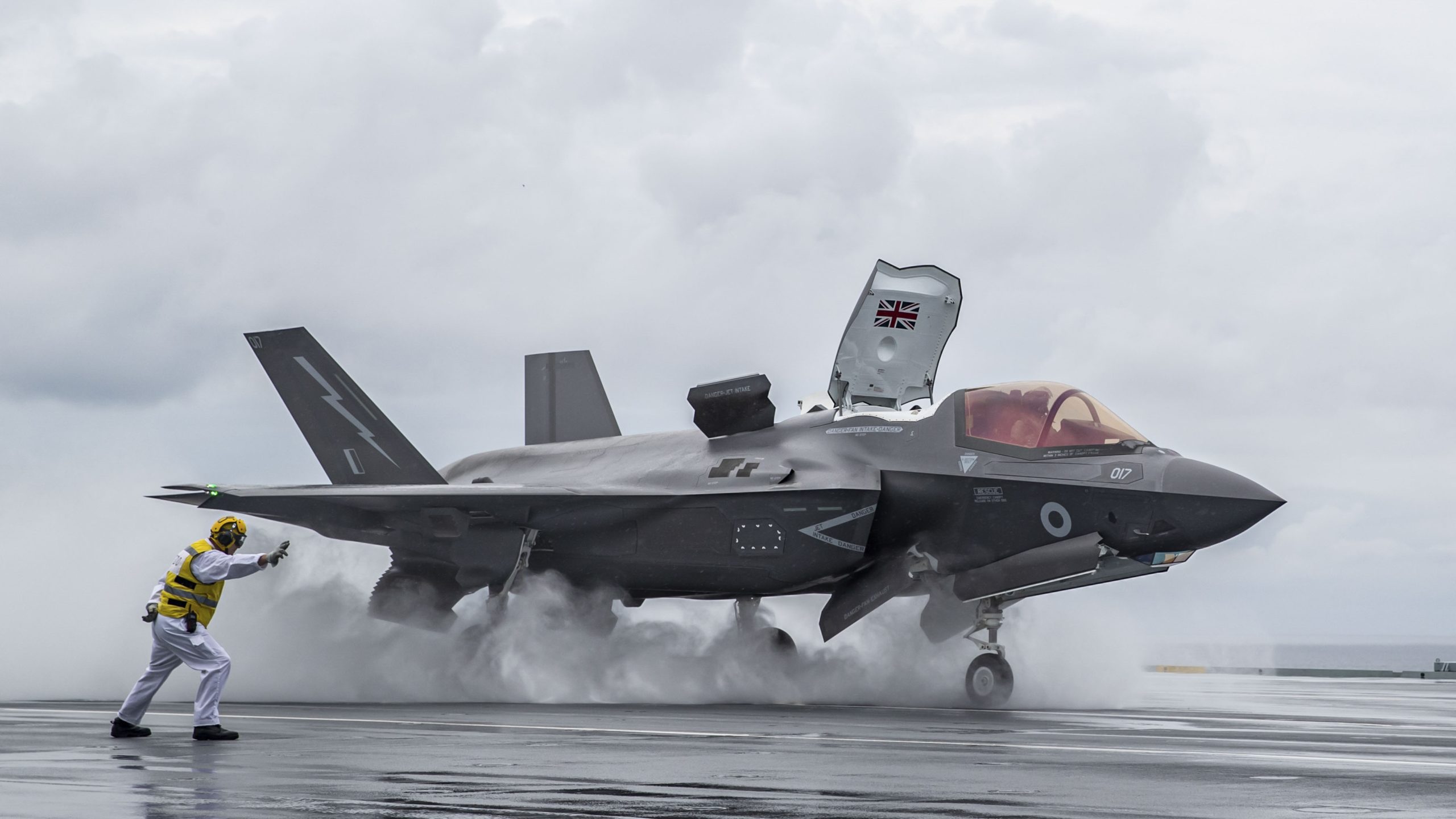
Overview: Experts in the design and development of the Queen Elizabeth-class aircraft carrier deck coating.
TRL9 Limited is the official subject matter experts in the design and development of the Queen Elizabeth-class aircraft carrier deck coating. The coating system enables the short-take-off and vertical-landing of F35C Lightening Strike fighter jets on the Queen Elizabeth and Prince of Wales aircraft carriers. This ground-breaking and patented technology is capable of withstanding thermal shock from ambient temperatures to 1,000°C in 11 seconds. The sealed, metallic coating is applied by thermal metal spray and provides a non-skid, gas-wash resistant coating which is currently deployed on both ships and has completed hundreds of successful landings.